CNC Machining: The Future of Manufacturing Precision Components
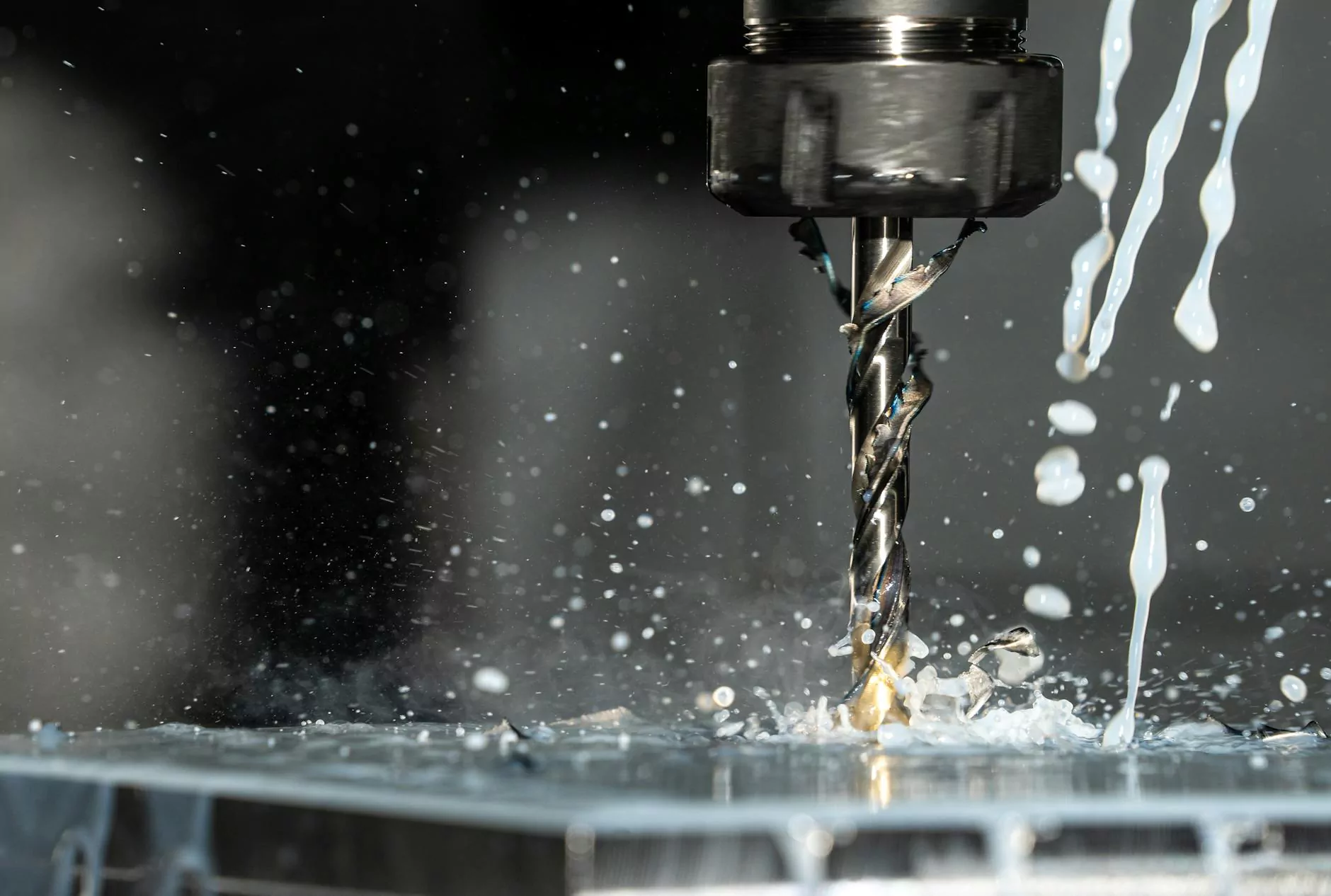
In today's fast-paced industrial landscape, businesses continually seek ways to enhance productivity and reduce costs. One of the most effective ways to achieve this is through precision manufacturing techniques. Among these, CNC machining has emerged as a game-changer, particularly in the production of lathe turned parts. This article dives into the intricacies of CNC machining and the role of a skilled lathe turned parts supplier, such as Deep Mould.
Understanding CNC Machining
CNC machining (Computer Numerical Control machining) refers to the use of computers to control machine tools. This technology allows for high precision, repeatability, and flexibility, making it ideal for industries that require finely crafted components.
- Increased Precision: CNC machines can produce parts with tolerances as tight as ±0.001 inches.
- High Efficiency: Once programmed, CNC machines can operate continuously, producing a large volume of components with minimal downtime.
- Versatile Materials: CNC machining can work with various materials, including metals, plastics, and composites.
The Process of CNC Machining Lathe Turning
The process of lathe turning incorporates several stages, each crucial to ensuring the end product meets the desired specifications:
- Designing the CAD Model: Engineers create detailed Computer-Aided Design (CAD) models that serve as blueprints for the parts to be manufactured.
- Setting Up the CNC Lathe: Technicians program the CNC machine with specific measurements, tool paths, and operations.
- Machining: The lathe uses rotating motion to shape the material into the desired form while cutting tools remove excess material.
- Finishing Touches: After the primary machining process, parts may undergo additional processes such as polishing or surface treatment.
Benefits of Partnering with a CNC Machining Lathe Turned Parts Supplier
Choosing a reliable cnc machining lathe turned parts supplier is pivotal for any business aiming to enhance its manufacturing capabilities. Here are several compelling reasons why partnering with experts like Deep Mould can be advantageous:
1. Quality Assurance
Partnering with an established supplier ensures that you receive high-quality parts that meet industry standards. Deep Mould implements stringent quality control measures throughout the manufacturing process, which minimizes defects and guarantees durability.
2. Cost-Effective Solutions
Utilizing CNC machining technologies reduces production costs through efficient material usage and minimized waste. By selecting the right supplier, businesses can achieve a better return on investment (ROI) as all components are produced to stringent specifications, eliminating the need for costly reworks.
3. Rapid Prototyping
One of the remarkable features of CNC machining is the speed at which prototypes can be developed. Suppliers such as Deep Mould can transform design files into physical prototypes in a matter of hours or days, facilitating quicker product development cycles.
4. Design Flexibility
CNC machining allows for great flexibility in design. Whether you need bespoke geometric shapes or a series of complex features, a competent supplier can adapt to various design requirements, enabling businesses to innovate without constraints.
5. Scalability
As your business grows, so too can your production volumes. A proficient CNC machining lathe turned parts supplier can seamlessly scale production up or down to match demand, providing crucial agility in today’s evolving markets.
Key Industries Benefiting from CNC Machining Lathe Turned Parts
Today, the applications for CNC machining are extensive, with several industries reaping significant benefits:
- Aerospace: Precision components are vital for safety and performance.
- Automotive: Manufacturers require high-quality parts for assembly lines.
- Medical: Biocompatible components and devices demand exacting standards.
- Electronics: Intricate parts are essential for efficient function and durability.
Material Options for CNC Machining
Choosing the right material for CNC machining is critical for achieving the desired functionality and performance of the components. Some commonly used materials include:
- Aluminum:
- Lightweight and corrosion-resistant, aluminum is ideal for various applications.
- Stainless Steel:
- Known for its toughness and resistance to rust, making it perfect for medical and automotive uses.
- Brass:
- Offers excellent machinability and conductivity, often used for fittings and electrical components.
- Plastics:
- Lightweight and versatile, plastics can be machined to meet numerous industrial needs.
Quality Control Measures in CNC Machining
Quality is paramount in the manufacturing industry, and CNC machining is no exception. At Deep Mould, a variety of quality control measures are implemented to ensure that all lathe-turned parts meet the highest standards:
- Dimensional Inspection: Utilizing advanced measurement technology like CMM (Coordinate Measuring Machines) to ensure accurate dimensions.
- Material Verification: Testing materials to confirm they meet specified standards and properties.
- Process Audits: Regularly reviewing manufacturing processes to identify any potential areas for improvement.
- Final Inspection: Before shipping, each part undergoes a final quality check to ensure it meets customer specifications.
Future Trends in CNC Machining
The CNC machining industry is constantly evolving, influenced by advancements in technology and the changing needs of businesses. Several notable trends are shaping the future of CNC machining:
1. Increased Automation
The integration of robotics in CNC machining is on the rise. Automation not only improves efficiency but also enhances safety and reduces labor costs.
2. Additive Manufacturing
Hybrid manufacturing techniques that combine traditional CNC machining with additive processes (3D printing) are becoming more common, allowing for more complex designs and reduced waste.
3. Smart Manufacturing
The application of IoT (Internet of Things) in CNC machinery enables real-time monitoring and data analysis, resulting in optimized performance and predictive maintenance solutions.
Conclusion
In the realm of precision manufacturing, choosing a trusted cnc machining lathe turned parts supplier is crucial for attaining high-quality components that meet your operational needs. With an impressive array of benefits including enhanced quality, efficiency, and design flexibility, CNC machining stands out as a preferred solution for numerous industries. At Deep Mould, we are committed to providing exceptional service and unparalleled craftsmanship to help your business thrive in a competitive marketplace. Partner with us today and experience the future of manufacturing excellence!